The Power of Prototype Molding in Modern Business
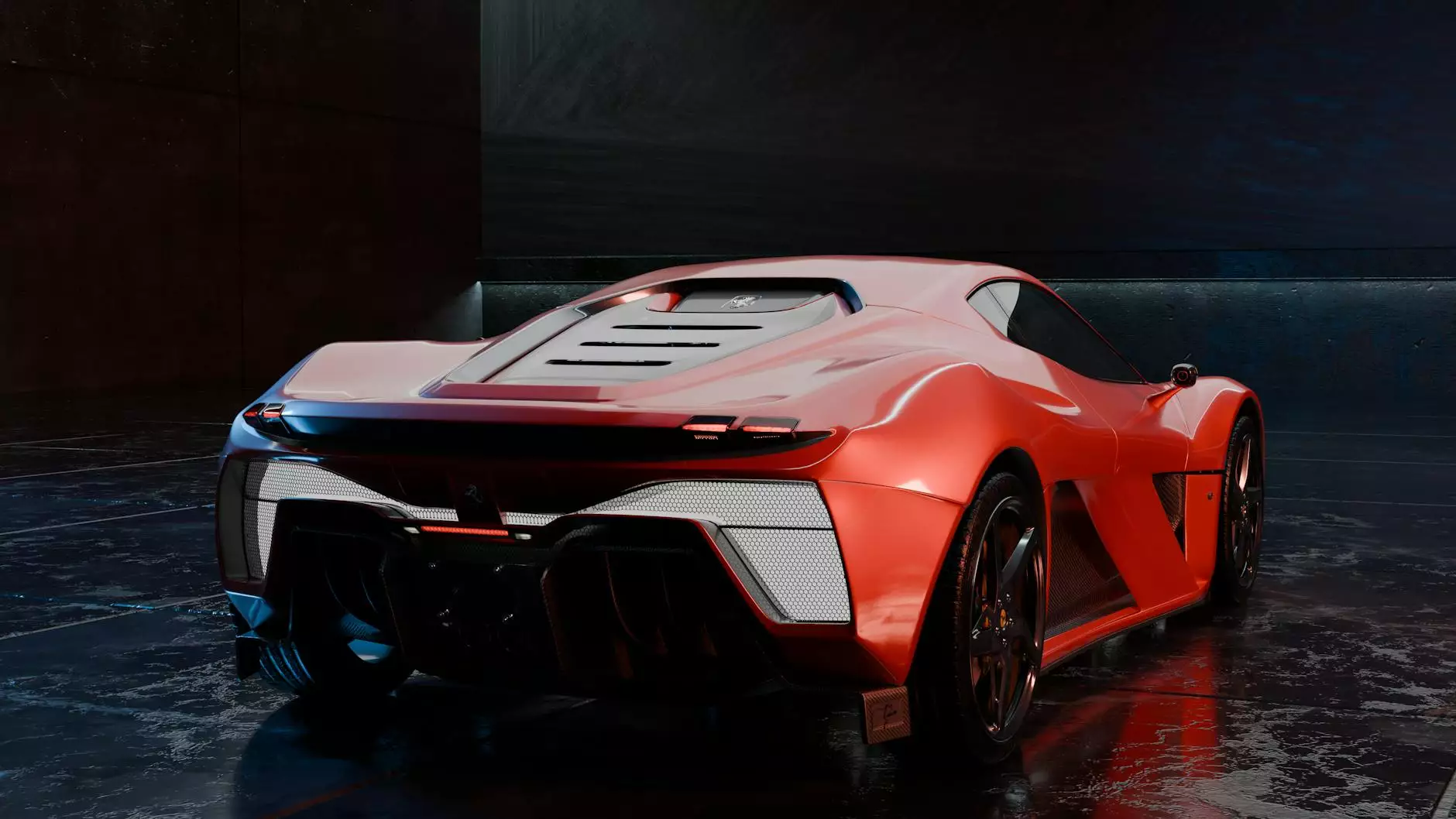
In today's rapidly evolving industrial landscape, businesses must adapt and innovate to stay ahead of the competition. One of the most essential processes that enable such innovation is prototype molding. This technique plays a pivotal role in the development of new products, particularly in the field of metal fabrication. In this article, we will delve deep into the world of prototype molding, its advantages, applications, and how it can revolutionize business practices for companies like DeepMould in the Metal Fabricators sector.
Understanding Prototype Molding
Prototype molding refers to the process of creating a prototype of a product using molds. Traditionally, this method has been utilized in various industries, including automotive, aerospace, and consumer goods, to develop models that can accurately represent the final product. The essence of prototype molding lies in its ability to validate designs and concepts quickly and cost-effectively.
The Importance of Prototyping in Product Development
Prototyping is crucial in product development for several reasons:
- Design Verification: Prototypes allow designers to test their concepts and make adjustments before moving into full-scale production.
- Cost Efficiency: By identifying design flaws early, businesses can save significant costs associated with material waste and alterations during production.
- User Feedback: Physical prototypes enable companies to obtain feedback from users, which is essential for refining product features and enhancing user experience.
- Time Management: Rapid prototyping speeds up the development process, allowing businesses to bring their products to market faster than competitors.
Types of Prototype Molding Processes
There are several methods of prototype molding, each offering distinct advantages depending on the project's needs:
1. Injection Molding
Injection molding is one of the most popular methods of prototype molding. In this process, material (commonly plastic) is heated until it becomes liquid and then injected into a mold. The result is a highly accurate replica of the intended product. This technique is particularly useful for producing complex shapes and designs with high repeatability.
2. Blow Molding
Blow molding is primarily used for creating hollow objects, such as bottles and containers. The process involves inflating a heated plastic tube inside a mold to form the desired shape. This technique is advantageous for testing designs in industries like packaging.
3. CNC Machining
CNC (Computer Numerical Control) machining is another effective method for creating prototypes. It involves using computer-controlled machinery to remove material from a solid block to create precise shapes. This method is particularly advantageous for metal fabrication, allowing for intricate designs and high tolerances.
Advantages of Prototype Molding
The benefits of using prototype molding in product development are numerous. Here are some of the key advantages:
- Precision and Accuracy: Prototype molding techniques, such as injection molding and CNC machining, deliver high-precision prototypes that closely resemble the final product.
- Material Versatility: This process can utilize a wide variety of materials, including metals, plastics, and composites, enabling companies to choose the best options for their products.
- Reduced Risk: By validating designs through prototyping, businesses significantly mitigate the risks associated with product launch failures.
- Scalable Solutions: Prototype molding sets the stage for scaling up production. Once a prototype is tested and approved, manufacturers can easily transition to larger production runs.
Applications of Prototype Molding in Industry
The versatility of prototype molding allows it to be applied in various industries, enhancing productivity and innovation. Here are a few notable applications:
1. Automotive Industry
In the automotive sector, companies use prototype molding to create parts and components that require stringent performance specifications. Creating prototypes of car parts allows manufacturers to test aerodynamics, durability, and safety features before mass production.
2. Aerospace Industry
Aerospace engineering demands the highest levels of precision and reliability. Prototype molding processes enable engineers to test components under extreme conditions, ensuring they meet safety and performance standards before actual deployment in aircraft.
3. Consumer Electronics
The fast-paced consumer electronics industry benefits significantly from prototype molding. Rapid prototyping allows companies to iterate designs quickly based on user feedback, ensuring the final product meets consumer expectations and stands out in a competitive market.
4. Medical Devices
The medical device industry requires prototypes that comply with strict regulations. Through prototype molding, manufacturers can develop and test innovative medical solutions, such as surgical instruments, diagnostic equipment, and patient monitoring devices, ensuring they function correctly and safely.
How Prototype Molding Enhances Business Operations
For businesses, especially in the Metal Fabricators domain, prototype molding offers transformative advantages that can enhance operations at multiple levels:
1. Streamlined Product Development
By integrating prototype molding into their development processes, companies can streamline the pathway from concept to market. The ability to rapidly produce prototypes allows for faster iterations and approval cycles. This agility can significantly reduce time-to-market, giving businesses a competitive edge.
2. Improved Team Collaboration
Prototypes serve as tangible representations of ideas, facilitating better communication among design, engineering, and marketing teams. With a physical model to reference, teams can collaborate more effectively, leading to an enhanced understanding of the product and a unified vision for its development.
3. Enhanced Customer Satisfaction
By incorporating user feedback into the prototyping process, businesses can tailor products to meet customer demands more accurately. The outcome is a product that delights consumers, leading to increased satisfaction, loyalty, and ultimately, sales.
4. Cost Management
Although the initial investment in prototype molding may seem significant, the long-term savings are undeniable. Early identification of design flaws mitigates costly changes during mass production, optimizing overall costs while maintaining quality.
The Future of Prototype Molding
As technology progresses, the world of prototype molding continues to evolve. Advancements in materials science and manufacturing technology, including 3D printing and additive manufacturing, are set to revolutionize how prototypes are created. These innovations will enable even greater customization, efficiency, and sustainability in product development, paving the way for the next generation of industrial solutions.
Conclusion
In conclusion, prototype molding is an invaluable tool for businesses, especially within the Metal Fabricators sector. Its ability to enhance product development processes, reduce costs, and improve customer satisfaction makes it a crucial investment for companies looking to innovate and excel in today's competitive marketplace. Companies like DeepMould can leverage these advantages to position themselves as leaders in the industry, driving progress and delivering outstanding products to their customers.
Call to Action
Are you ready to take your business to the next level with prototype molding? Visit DeepMould today to learn how our expertise in metal fabrication and prototyping can help your company achieve its goals and stay ahead of the competition.