The Comprehensive Guide to Plastics Injection Molding
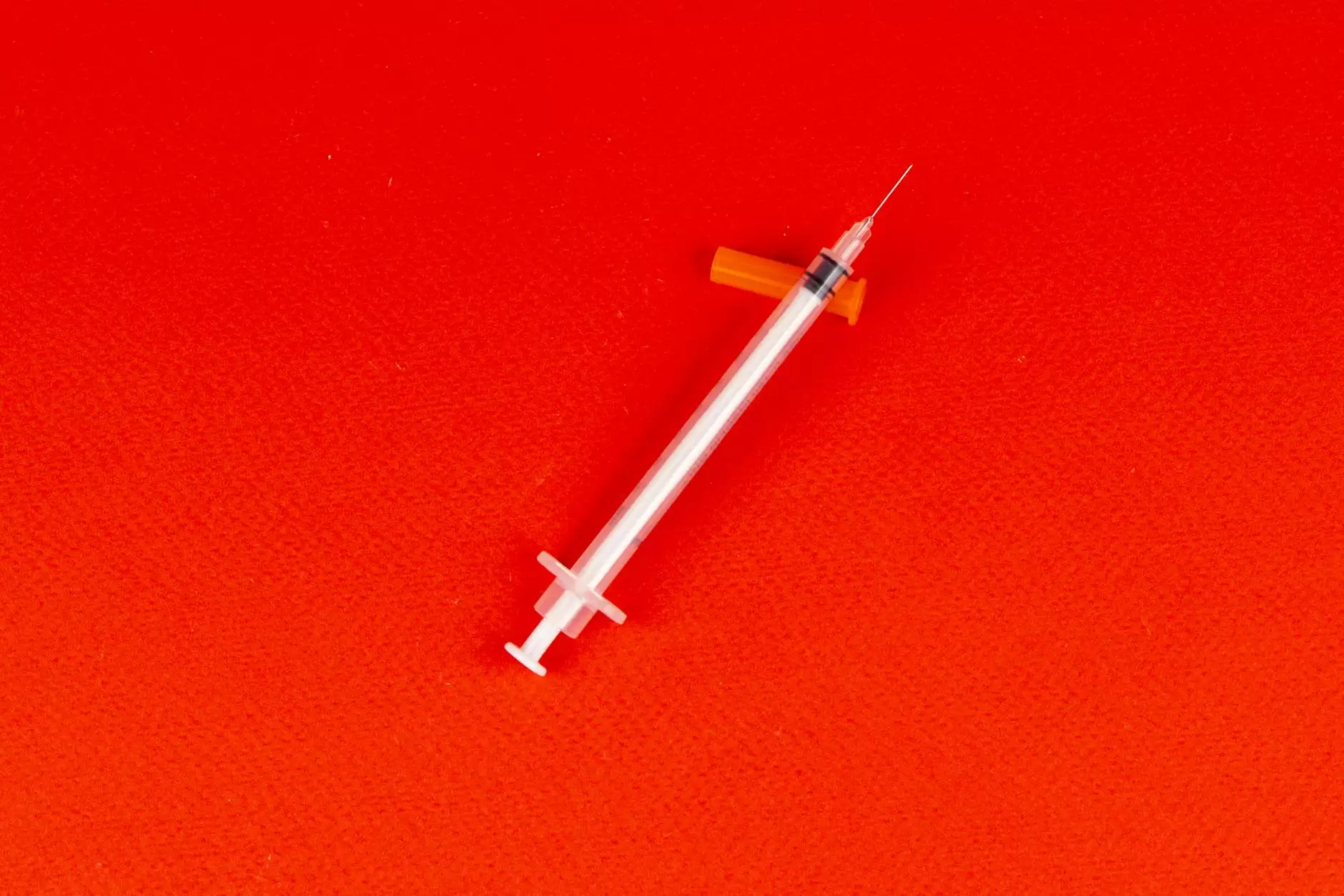
Plastics injection molding is a crucial manufacturing process in which molten plastic is injected into a mold to form various products. This methodology is highly favored due to its efficiency, scalability, and ability to produce intricate designs with precision. In this article, we will delve deep into the mechanics of plastics injection molding, its advantages, significant applications, and its relevance in metal fabrication, particularly at deepmould.net.
What is Plastics Injection Molding?
Plastics injection molding is a manufacturing process used to create parts by injecting molten material into a mold. Here's a straightforward breakdown of the process:
- Material Preparation: The raw plastic is fed into a heated barrel.
- Injection: The plastic is melted and injected into a mold under high pressure.
- Cooling: The plastic cools and solidifies into the shape of the mold.
- Ejection: After cooling, the newly formed part is ejected from the mold.
The Advantages of Plastics Injection Molding
Plastics injection molding offers numerous advantages, making it a preferred choice for manufacturers. Let's explore these benefits in detail:
- High Efficiency: Injection molding can produce a large number of parts in a short time, reducing manufacturing costs.
- Precision: The process can create highly complex and precise parts with tight tolerances.
- Material Versatility: A wide range of plastics can be used, including thermoplastics and thermosetting plastics.
- Scalability: Once a mold is created, it can be used for mass production with minimal additional costs.
- Reduced Waste: Injection molding uses only the necessary amount of material, minimizing waste during production.
Applications of Plastics Injection Molding
The applications of plastics injection molding are vast and span across various industries.
Automotive Industry
In the automotive sector, plastics injection molding is used to manufacture components like dashboards, instrument panels, and bumpers. The lightweight nature of plastics helps in improving fuel efficiency and reducing emissions.
Consumer Electronics
From smartphone cases to intricate electronic components, the consumer electronics industry heavily relies on injection molded parts. The ability to create complex shapes enables designers to push the boundaries of product design.
Medical Devices
Plastics injection molding is crucial in the production of medical devices, offering the ability to create sterile, precise components like syringes, surgical instruments, and more, while maintaining high hygiene standards.
Packaging Industry
The packaging industry benefits from injection molding in creating durable containers, caps, and other packaging solutions that protect products while ensuring they are user-friendly.
How Plastics Injection Molding Integrates with Metal Fabrication
At deepmould.net, we focus on the integration of plastics injection molding within the realm of metal fabrication. While these two processes may seem distinct, they often work hand-in-hand in the production of hybrid products.
For instance, metal components can be encapsulated in plastic parts to enhance durability or improve aesthetics. The synergy between metal and plastic not only reduces weight but also offers more functional designs.
Choosing the Right Manufacturer for Plastics Injection Molding
Selecting a qualified manufacturer is essential to ensure the success of your project. Here are some key considerations:
- Experience: Look for manufacturers with a proven track record in plastics injection molding.
- Quality Standards: Ensure they adhere to industry-specific quality standards, such as ISO certifications.
- Technological Capabilities: Modern machinery and technology can significantly impact the quality and efficiency of production.
- Customer Reviews: Testimonials and feedback from previous clients can offer insight into the manufacturer's reliability and quality.
Future Trends in Plastics Injection Molding
The future of plastics injection molding is poised for exciting developments. Here are some trends to watch:
- Green Manufacturing: As environmental concerns grow, manufacturers are seeking sustainable materials and processes to reduce their ecological footprint.
- Smart Manufacturing: The integration of IoT and AI technologies to optimize the production process and predictive maintenance will enhance efficiency.
- Customization: As consumer demand for personalized products rises, injection molding can adapt to create customized parts more easily.
- Advancements in Materials: Innovations in plastic materials, such as biodegradable plastics and composites, will broaden the applications of injection molding.
The Importance of Quality Control in Plastics Injection Molding
Maintaining quality control in the injection molding process is essential for producing high-quality products. Here are a few methods to ensure quality:
- Regular Inspections: Conduct routine inspections of the molds and machinery to detect any imperfections early on.
- Testing Procedures: Implement standardized testing procedures for each batch of produced parts to ensure they meet specifications.
- Employee Training: Regular training ensures that staff are continuously updated on best practices and new technologies.
Conclusion
In conclusion, plastics injection molding is an invaluable process that significantly contributes to various industries, including aerospace, automotive, healthcare, and consumer products. Its efficiency, versatility, and cost-effectiveness make it essential for modern manufacturing. At deepmould.net, we are dedicated to advancing the potential of plastics injection molding within the realm of metal fabrication and beyond. As we head into the future, embracing innovation and technology will be vital in meeting the evolving demands of the market.
For more information on how plastics injection molding can benefit your business, visit deepmould.net.