Understanding Injection Plastic Molding: The Future of Manufacturing
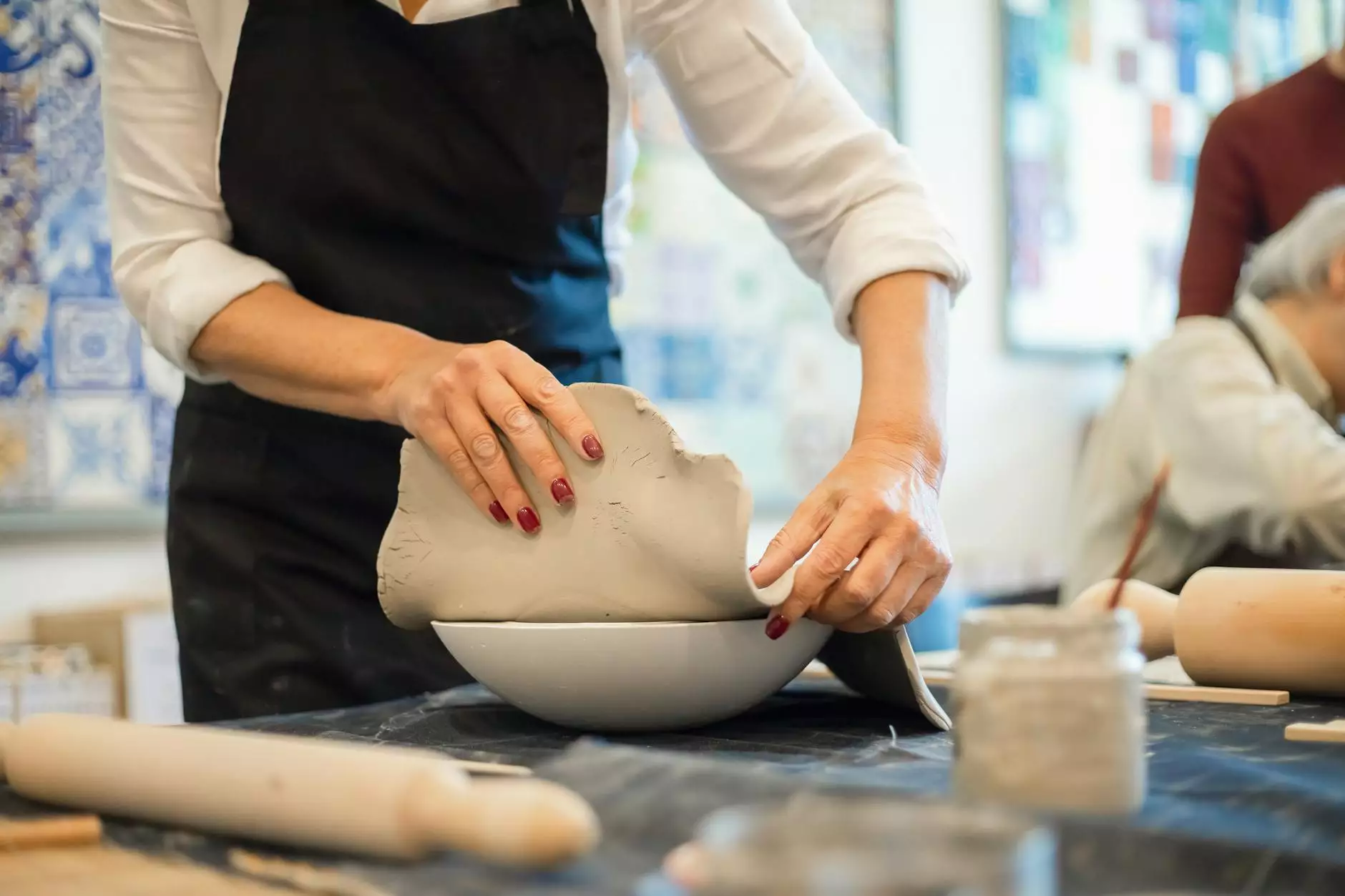
In today's fast-paced industrial landscape, injection plastic molding has emerged as a cornerstone technology fueling innovation across various sectors. As we dive into the depths of this dynamic process, we will uncover its significance, advantages, and how businesses like DeepMould.net leverage it to excel in the competitive world of manufacturing.
What is Injection Plastic Molding?
Injection plastic molding is a manufacturing process for producing parts by injecting molten material into a mold. This versatile process is utilized predominantly in the production of plastic parts, making it integral to a wide array of industries. The materials often used in this process include various types of thermoplastics and thermosetting polymers.
The Process Explained
Let’s break down the injection molding process into its essential steps:
- Material Selection: The journey begins by selecting the right polymer material for the specific product requirements. Common materials include ABS, polycarbonate, and nylon.
- Heating: The selected plastic pellets are fed into a heated barrel where they are melted and homogenized into a consistent molten state.
- Injection: The molten plastic is injected into a precisely engineered mold under high pressure.
- Cooling: Once the mold is filled, the material cools and solidifies, taking the shape of the mold cavity.
- Mold Opening and Product Ejection: The mold is opened, and the final product is ejected. This step may involve secondary operations to remove excess material (flash).
Benefits of Injection Plastic Molding
The advantages of using injection plastic molding are manifold, making it a preferred choice for manufacturers:
- Cost-Efficiency: For large production runs, the cost per unit decreases significantly, making it economically viable for mass production.
- Precision and Consistency: The ability to create highly detailed and accurate parts consistently is paramount in sectors such as automotive and medical.
- Material Versatility: A variety of materials can be used, allowing for a high degree of customization and flexibility in product design.
- Reduced Waste: The process is designed to minimize waste, producing little excess material, which enhances overall sustainability.
- Rapid Production Speed: Compared to traditional manufacturing methods, injection molding allows for quicker production cycles, meeting market demand efficiently.
Applications of Injection Plastic Molding
The versatility of injection plastic molding is reflected in its broad range of applications across various industries:
1. Automotive Industry
In the automotive sector, injection molded parts are used extensively, including components like dashboards, wheel covers, and housing for lighting systems. The lightweight nature of molded plastics helps improve fuel efficiency.
2. Consumer Electronics
Devices such as smartphones, laptops, and wearable tech rely on injection molded parts for housing and enclosures, ensuring ruggedness and aesthetic appeal.
3. Medical Devices
Medical instruments, syringes, and drug delivery devices often use injection molded components, ensuring sterility and precision in design.
4. Household Products
From containers to appliances, everyday household items often utilize injection molded plastics due to their functionality and cost-effectiveness.
Choosing the Right Partner for Injection Plastic Molding
When it comes to leveraging injection plastic molding for your enterprise, selecting a competent partner is crucial. A few factors to consider include:
- Experience and Expertise: Opt for manufacturers with extensive industry knowledge and a proven track record.
- Technological Capabilities: Ensure they utilize the latest technology and equipment to enhance efficiency and quality.
- Customization Options: A strong partner should be able to offer tailored solutions, matching your exact specifications and requirements.
- Sustainability Practices: Evaluate their processes to ensure they prioritize sustainability and environmental responsibility.
Quality Assurance in Injection Plastic Molding
Quality control is a critical aspect of injection plastic molding. Manufacturers implement stringent quality assurance protocols to ensure that each part meets the required standards. Essential practices include:
- Regular Mold Testing: Ongoing assessments of molds are necessary to detect wear and tear and ensure precise specifications are maintained.
- Material Testing: Testing the raw materials for defects and ensuring they meet industry standards before entering the production line.
- Final Inspection: After production, a thorough inspection of each part is conducted to ensure compliance with dimensional and aesthetic standards.
Sustainability in Injection Plastic Molding
As industries strive for sustainable solutions, injection plastic molding plays a vital role by:
- Using Recyclable Materials: Many modern plastics used in injection molding are recyclable, reducing their environmental footprint.
- Minimizing Waste: Advanced techniques in molding reduce excess material usage, promoting sustainability.
- Energy Efficiency: Innovations in technology have led to more energy-efficient machines that lower overall energy consumption during production.
The Future of Injection Plastic Molding
As we look ahead, the future of injection plastic molding is promising, with emerging trends including:
- Automation and AI: Integrating AI technologies for predictive maintenance and optimization of the molding process is on the rise.
- Smart Manufacturing: The adoption of IoT in molding processes enhances monitoring and real-time adjustments for maximum efficiency.
- Bioplastics: The shift towards bioplastics is reshaping the industry by offering more sustainable material options.
Conclusion
In summary, injection plastic molding is a revolutionary manufacturing process that continues to evolve, providing significant benefits across diverse industries. By choosing a knowledgeable partner committed to quality and sustainability, businesses can harness this technology to innovate and thrive. The future is bright for companies that are ready to embrace the potential of injection molding, especially in an era that increasingly prioritizes efficiency and environmental responsibility.
For more information on how DeepMould.net can assist your business with cutting-edge injection plastic molding solutions, visit DeepMould.net today!